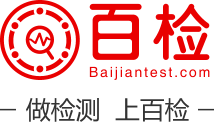
经历了10年两位数高速增长后,中国汽车市场转入平稳增长,中国汽车工业协会*新统计数据显示,上半年中国汽车产销表现平平,汽车产销分别为1209.5万辆和1185.03万辆,同比增长2.6%和1.4%,预计全年汽车销量同比增长3%。从平均增速24%到7%,再到可能出现的3%,中国汽车市场从高速增长转入微增长已是事实。在车市低迷、众多车企销量滑落的大环境下,部分合资企业却逆势回升,成为车市寒流中的一抹亮色。
其中,广汽丰田2015年1-7月销量达到233,525辆,同比增幅24.3%。凭借远超大盘的增速,广汽丰田成为逆势增长的车企代表。
业内人士分析认为,新车效应固然是今年车企销量增长的原因之一,但不同阵营“此消彼长”的背后,苦练内功形成的体系竞争力,则是更重要的屏障。
品质助力销量上扬
2015年初以来,我国车市经历众多车企发起官方降价潮、促销潮,很多车企都遇到的增速放缓的尴尬。
在中国车市整体低迷的情况下,广汽丰田取得了不俗的增长,跑赢大盘,取得亮眼的增长业绩。
上半年,广汽丰田接连推出全新凯美瑞、全新汉兰达和进口全新埃尔法三款新车,均成为市场“大热门”。
年初上市的全新凯美瑞,一直稳居同级前三,7月更是夺得中**车销量**。“豪华大7座SUV”全新汉兰达4月上市后持续热销,目前累计销量30,685辆。新汉兰达将会成为广汽丰田的主力产品,广汽丰田也将逐步提高汉兰达的产能,到今年年底,广汽丰田可能在销量上还会有一定增长。雷凌和致炫两款中小型车也深受热捧,广汽丰田所打造的“中小型车战略”成功开局。综合来看,广汽丰田对年初所制定的2015年40万辆的目标志在必得。
广汽丰田逆势领跑并不出人意料,多年来高可靠性、高保值率、低故障率的直观印象与丰田品牌本身有着*大的重合度。凯美瑞与汉兰达在各自细分市场创造的品质口碑也成为广汽丰田的重要支撑。
2014年J.D.Power发布的中国新车质量研究(IQS)报告中,广汽丰田排名合资品牌**。汉兰达和逸致一举摘下各自细分市场的桂冠。凯美瑞作为丰田全球战略车型,赢得了1700万车主,其品质可靠性更是有口皆碑。
深受消费者认可的产品品质,是广汽丰田能够保持稳健增长的重要基石,而这也是广汽丰田自成立以来便矢志不渝所追求的重中之重。
早在2004年成立之初,广汽丰田就把品质作为企业长远发展*重要的战略保障。
“品质是生产出来的,而不是检测出来的”,广汽丰田始终把这句话视为信仰,在生产的每一个环节中都严格把控。例如,丰田所打造的举世闻名的品质保障系统——“安东”拉绳。任何一个员工若发现问题,都有权利拉动身旁的安东拉绳,及时停止可能出现错误的生产,立即解决问题、消除不良,不让一件不良品流入下一道工序,保证每个工序的品质。
为了打造精益求精的品质,广汽丰田在看似繁杂的细节不断提高和超越自身。比如,在总装车间引入了自动防错装置,它可以检测到螺旋螺母的拧紧作业的数量和扭矩是否符合标准值,显示绿灯就是按照要求完成了作业,红灯则表示拧紧数量或者扭矩不符合要求,这样的装置能够帮助员工**时间发现问题,并改善作业以达到标准。细节决定成败,在每一个工序、每一个细节都做到尽善尽美,这些正是广汽丰田品质保障的关键要领。
丰田全球品质保证监测机构每年都会对全球各家工厂进行长达一个月的品质监测,并且基于一套完善的车辆品质管理标准,同时制定了全球统一的监测标准。检测全面多达几千项,另外数名专家每天仅检测一台车,其中包括在强光下发现外观微凹检测项目,这种精细的检测在行业内达到严苛标准。在多达数千项严格乃至苛刻的“考验”下,广汽丰田屡获佳绩。在2012-2014年,广汽丰田两条生产线先后获得丰田全球*高评价,这意味着,在对待品质保持一致高标准和严要求的丰田全球工厂体系中,广汽丰田的制造品质都是拔尖的。
《中国制造2025》是中国从制造大国迈向制造强国的战略纲领,它将“质量为先”作为重点方针之一。从大到强,就必须由追求高数量向谋求高品质转变。在品质上占据优势的企业才能成为制造强国的中流砥柱。在汽车行业,品质可靠性上的优势成为广汽丰田逆势领跑的内因,也成为广汽丰田长期稳健发展的惯性动力。
体系支撑智造**
如果说品质是汽车制造企业安身立命的根基所在,那么智能制造水平则是未来竞争力较量的重要砝码。
以信息技术与制造技术深度融合为特征的智能制造模式,正在引发整个制造业的深刻变革。“中国制造2025”明确指出要将智能制造作为主攻方向,推进制造过程的智能化,深化互联网在制造领域的应用。
作为丰田21世纪全球模范工厂,广汽丰田导入了全球**的设备和技术,生产过程实现较高程度的自动化。焊装车间导入丰田GBL(GLOBAL BODY LINE)线,所运用的机器人共计754台,自动化程度达58%。尤其是**引进的多轴蛇型机器人和新型焊枪,能以更小的空间占用和更低的能耗,实现****的焊接品质。GBL线还引入了代表****技术的“内侧夹紧装夹技术”,在确保车身精度的同时,在生产节拍内进行车型切替,真正实现柔性生产。
而在总装车间导入了先进的“SPS系统”(精细的零件分拣系统),使得零件区与装配区分离,将零部件的筛选与生产线的安装分开,使得生产线工人可以专注于精确的安装。优化的物流系统使物流线路更短,生产效率更高。
在科技改变世界的今天,虽然自动化的机器人已经承担了车间里的大部分工作内容,但“人”依旧是广汽丰田认为*为重要的组成部分。广汽丰田所实施的生产“自働化”,就是人字旁的自动化,主张人与机器协调互补,从而达到生产高品质产品的目的。在生产过程中,机器设备的保养、点检以及安东系统的运用都离不开人与机器的配合,而两者的配合更为“智能制造”增添了一份可靠与保障。
广汽丰田还坚持实施”准时化“方针,即在你所需要的时间和需要的地点向你提供所需要的东西,就是保持物质流和信息流在生产中的同步化。实行准时化,既可以减少库存、缩短工时,也能提高生产效率。
“自働化”和“准时化”,是广汽丰田实施丰田精益生产方式的两大支柱,它们其实与智能制造的思想非常吻合
与此同时,得益于于良好的内部机制,员工的创造力和主观能动性在广汽丰田也得到了充分的发挥,更是让“智能制造”如虎添翼。
在广汽丰田涂装车间涂装二科的喷涂区,共有12台中涂机器人,在第二生产线投产初期产量还不大的时候,中涂生产节拍比设计值慢,所以使用全部机器进行喷涂,导致了喷涂节奏慢单台机器人等待时间长。后来经过一线员工的研究,提出了改善提案,将中涂机器人台数减少为6台,另外6台备用、按需作业。在加快机器人动作、维持喷涂节奏不变的情况下,能使涂料的损耗量以及机器人的用电消耗下降了一半,这不仅减少了机器人的作业等待时间,也提高了喷涂效率。
这样的案例在广汽丰田工厂内并不罕见。迄今为止广汽丰田的员工累计提交的创意提案超过96万件,人均提案数量连年增长,涉及品质、工艺、安全、环境各个方面,为广汽丰田节省了不计其数的时间和金钱成本,更重要的是,它激发了企业的活力,让员工的创造性得到*大的发挥。
拥有全球**自动化生产线的同时,并不轻视人的创造力,这是广汽丰田制造体系的独特之处。用先进机械提升工艺水准,用严格的品质检查规范保证产品质量,用人的创造力打造“智能制造”的整套体系。
作为推动中国从制造大国到制造强国转变的重要战略纲领,“中国制造2025”是一个全面系统的规划,是从局部实力增强向体系竞争力提升的全面进化。作为制造业大户的汽车行业,在具备良好的制造基础之上,已经进入比拼体系竞争力的阶段。车市低迷而能逆势增长,并不存在什么捷径,其实是广汽丰田苦练内功的结果:坚持将高品质作为企业发展的根基并持续不断地改善,不只是用自动化机器而是充分发挥人的创造力来推进智能制造,都扎扎实实地提升了企业的竞争力。广汽丰田的“质造”和“智造”的双管齐下,无疑为汽车行业提供了一个优秀的体系范本。